Have you ever wondered how the food you buy at the store stays clean and safe to eat? Food factories work very hard to make sure everything is safe. One big way they do this is by using special disposable clothes. Let’s learn why food factories need things like suits, hats, and masks, and why they buy new ones all the time.
1. Keeping Food Super Clean
The most important job in a food factory is keeping the food safe from germs and other things that could make people sick.
- Stopping Germs: Workers can carry tiny germs on their clothes or skin. Special disposable suits cover their regular clothes. This stops germs from spreading to the food.
- No Hair Allowed: Imagine finding a hair in your food! Factories use disposable hats or hair nets to keep workers’ hair covered. This prevents hair from falling into the food mixture. You can find gear like disposable hair nets for cooking used for this.
- Blocking Sneezes: If a worker coughs or sneezes, disposable masks help catch the droplets. This keeps the air and the food clean. Simple blue disposable face masks are often used.
- Dust and Dirt: Factories can have dust or small bits from the food making process. Disposable clothes help keep this dust off the workers and away from the food.
2. Keeping Workers Safe Too
These special clothes don’t just protect the food. They also protect the workers.
- Splashes and Spills: Making food can sometimes be messy. Disposable clothes, like disposable suits for the food industry, protect workers’ skin and clothes from splashes of liquids or food bits.
- Dry Ingredients: Working with flour, sugar, or spices can create dust. Masks help workers not breathe this dust in. Suits keep the powder off their clothes.
3. Why Use Disposable Clothes?
Why not just wash regular clothes really well? Disposable clothes have big benefits for food safety.
- Always Clean: Every time a worker puts on a new disposable item, it’s perfectly clean. There’s no worry about old germs or dirt left over from washing.
- Easy and Quick: Workers can just put on new clothes and throw them away when done. This saves time and makes sure rules are followed easily.
- Following Safety Rules: Many places have strict rules about food safety. Using disposable protective gear helps factories follow these rules and pass inspections.
4. What Kinds of Clothes Do They Use?
Food factories use several types of disposable gear:
- Coveralls/Suits: Full body suits that cover clothes.
- Hats/Hair Nets: To keep hair contained.
- หน้ากากอนามัย: To cover the mouth and nose.
- Shoe Covers: To keep floor dirt from spreading. Check out these disposable shoe booties.
- Sleeve Covers: Extra protection for arms.
5. Why Buy These Every Year?
Factories often place large orders for these supplies once a year. Why?
- Never Running Out: Food safety is too important to run out of clean gear. Buying a year’s supply helps make sure they always have enough on hand.
- Planning Money: Buying in large amounts helps the factory plan its spending for the year. It can sometimes get them a better price too.
- Ready for Anything: Having plenty of supplies means they are ready for busy times or unexpected needs.
In short, food factories buy disposable suits, hats, and masks every year to keep food safe, protect workers, and follow important safety rules. Using new, clean gear every time is a simple and effective way to prevent problems and make sure the food we eat is healthy.
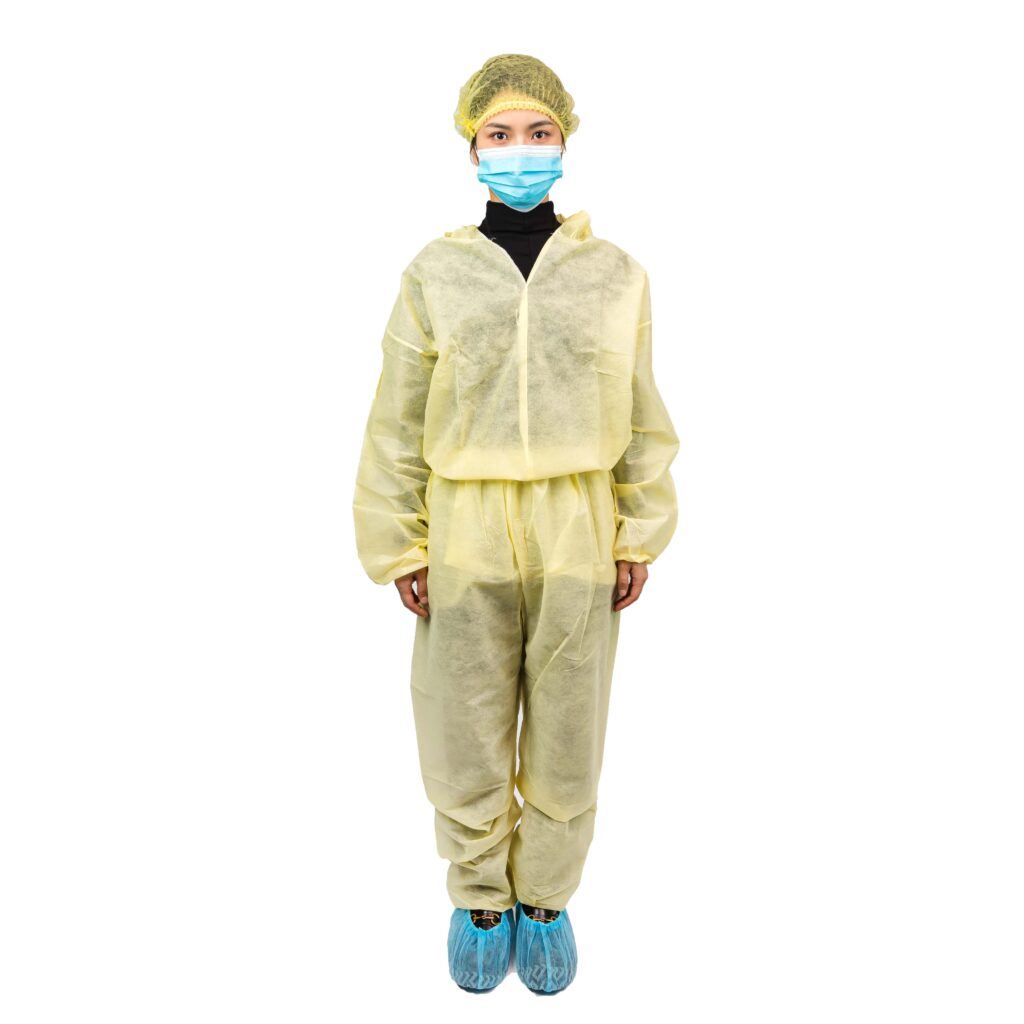