The current global climate has put a spotlight on the urgent need for Personal Protective Equipment (PPE). When it comes to disposable PPE coveralls, there’s more than meets the eye. It’s not just about finding a supplier. It’s about ensuring every piece of gear serves its protective purpose flawlessly. So, how do businesses manage the complex act of bulk buying these crucial items?
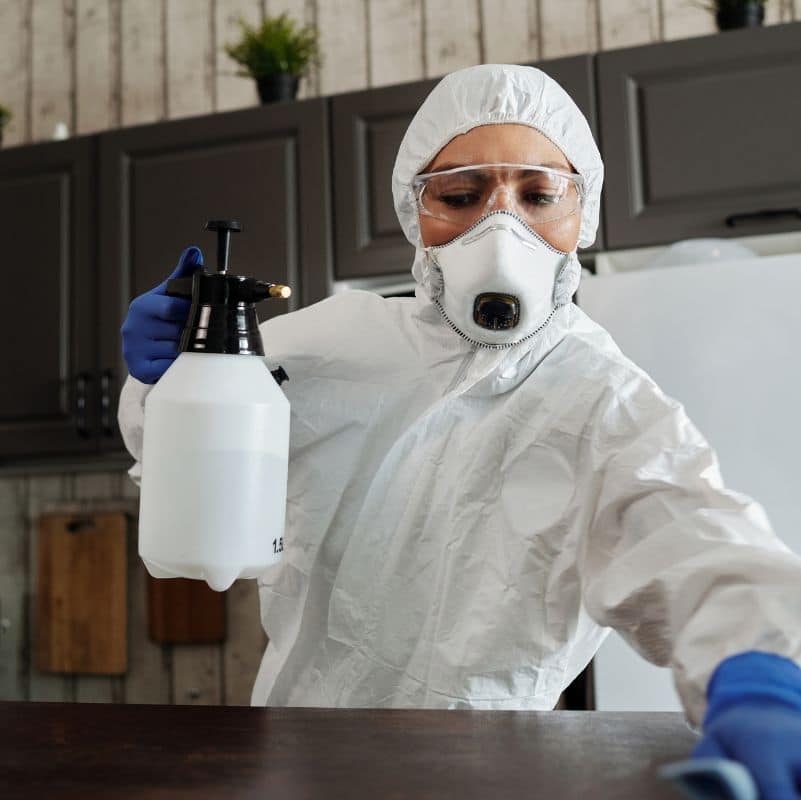
The Growing Demand for Disposable PPE Coveralls
Ever noticed how a thunderstorm can change the landscape? Similarly, the recent global health concerns reshaped industries, pushing the demand for disposable PPE coveralls to the forefront. Businesses, hospitals, and even local governments are now in dire need of large quantities of these protective garments.
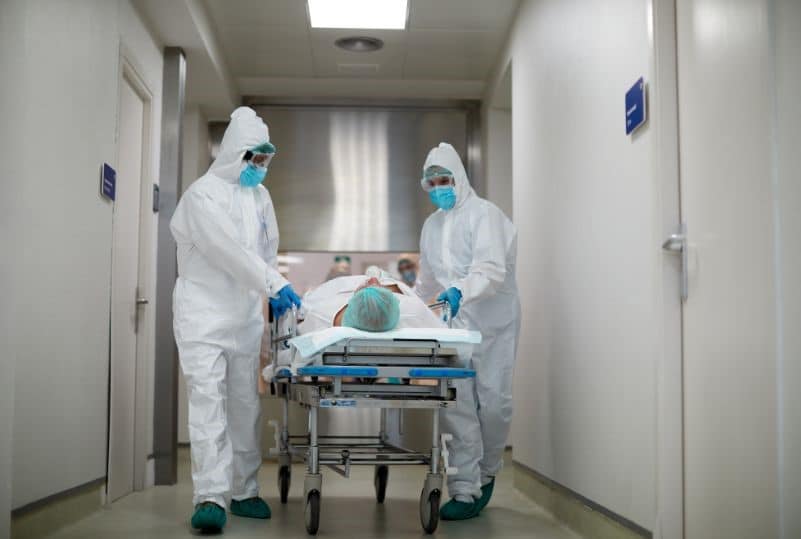
Why Bulk Procurement is a Viable Option
Think of bulk buying like buying a year’s worth of groceries in one go. Sounds daunting, right? But consider the benefits: potentially lower prices per unit, fewer trips to the market, and an assurance of stock. In the PPE scenario, it means reduced costs, consistent supply, and meeting urgent demand.
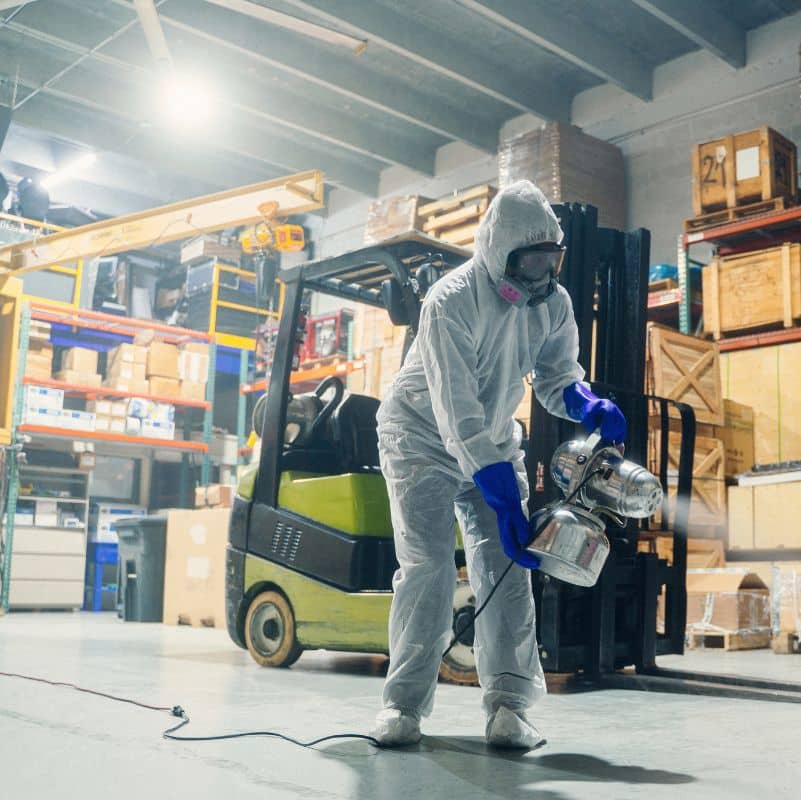
Challenges Faced in Bulk Procurement
However, it’s not all sunshine and roses. Just as buying groceries in bulk can lead to storage issues and potential waste, bulk procurement of PPE has its challenges. These can range from storage dilemmas to ensuring every single coverall matches the quality benchmark.
Steps to Ensure Quality in Bulk Orders
Vetting Potential Suppliers
Imagine entrusting someone with your favorite plant. You’d want to ensure they’d care for it, right? Similarly, not all suppliers are cut from the same cloth. It’s essential to dive deep into a supplier’s track record, their reviews, and perhaps even visit their production facility.
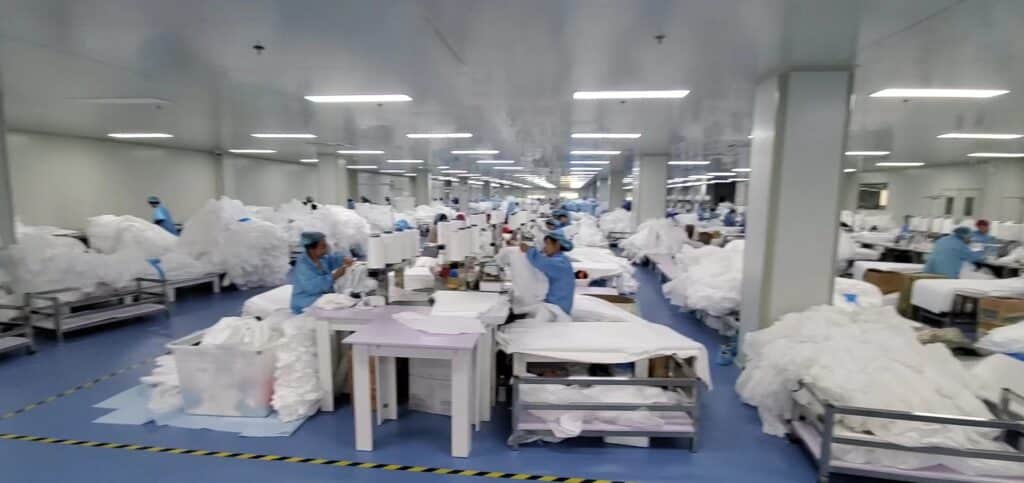
Conducting Quality Checks
Remember the adage, “Trust but verify”? It’s particularly apt here. Post-procurement, rigorous quality checks are vital. It might be checking for the correct material thickness, ensuring stitching is robust, or verifying the protective capabilities.
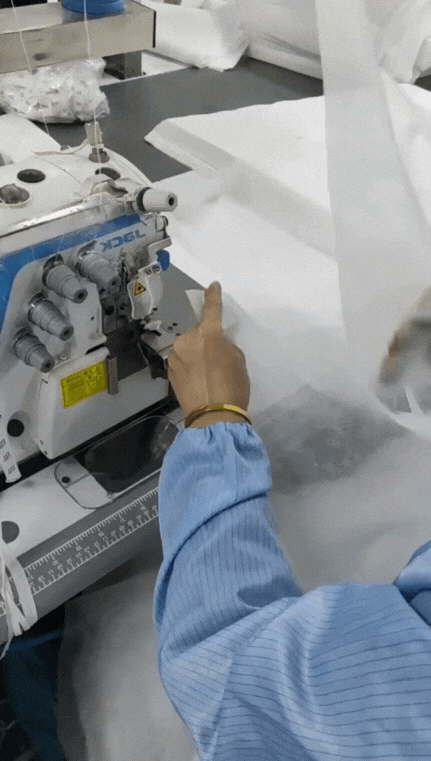
Achieving Quantity without Compromising on Quality
Maintaining a Consistent Supply Chain
A broken chain cannot hold weight. Maintaining a smooth supply chain, from order to delivery, is critical. This includes ensuring timely transportation, efficient customs clearance for international orders, and rapid distribution.
Leveraging Technological Tools for Quality Control
Enter the 21st century, where tech comes to our rescue. Using AI-driven quality control tools or tracking software can help businesses keep a close eye on their bulk orders, ensuring consistency and quality.
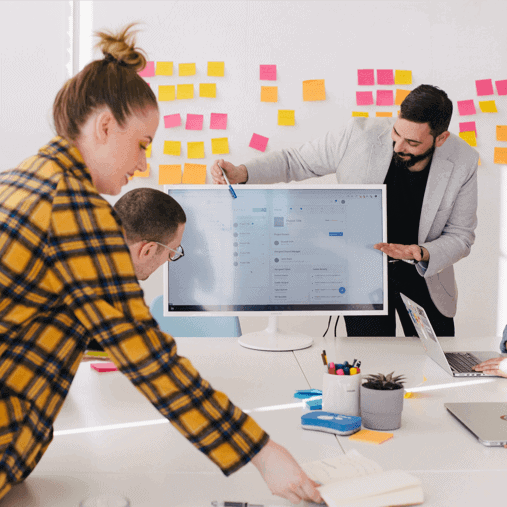
Conclusion: The Balancing Act of Bulk Procurement
Juggling quantity and quality might seem like a Herculean task. But with the right strategies, a dash of technology, and a sprinkle of diligence, businesses can master the art of bulk procurement.
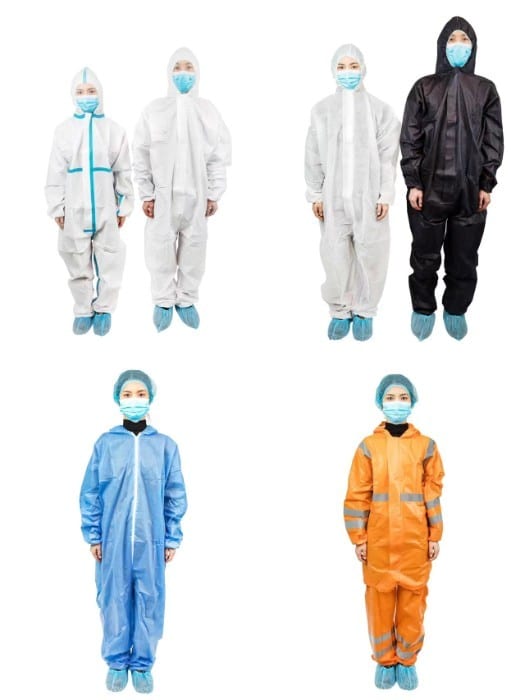
FAQ
1. What are the primary challenges in bulk procurement of PPE coveralls?
- Along with ensuring quality and quantity, businesses often grapple with logistical issues, customs clearances, and potential supplier inconsistencies.
2. How can one vet potential suppliers effectively?
- Apart from checking reviews and track records, one can also ask for sample products, visit production facilities, and engage third-party quality check agencies.
3. Are there any specific technological tools for PPE quality control?
- Many businesses now leverage AI-driven tools and software that allow real-time monitoring of production, ensuring that quality benchmarks are consistently met.
4. How important is it to maintain a consistent supply chain in bulk procurement?
- A consistent supply chain is paramount. It ensures timely delivery, adherence to quality standards, and can significantly reduce unforeseen challenges.
5. Can one achieve a balance between cost-effectiveness and quality in bulk procurement?
- Absolutely. While bulk orders often provide cost benefits, this doesn’t mean compromising on quality. With thorough vetting and consistent quality checks, businesses can achieve this balance.