Introduction
In the past few years, the face mask factory has become a focal point of public interest. As the world grapples with the COVID-19 pandemic, the use of face masks has become commonplace in public places, highlighting the necessity of these factories.
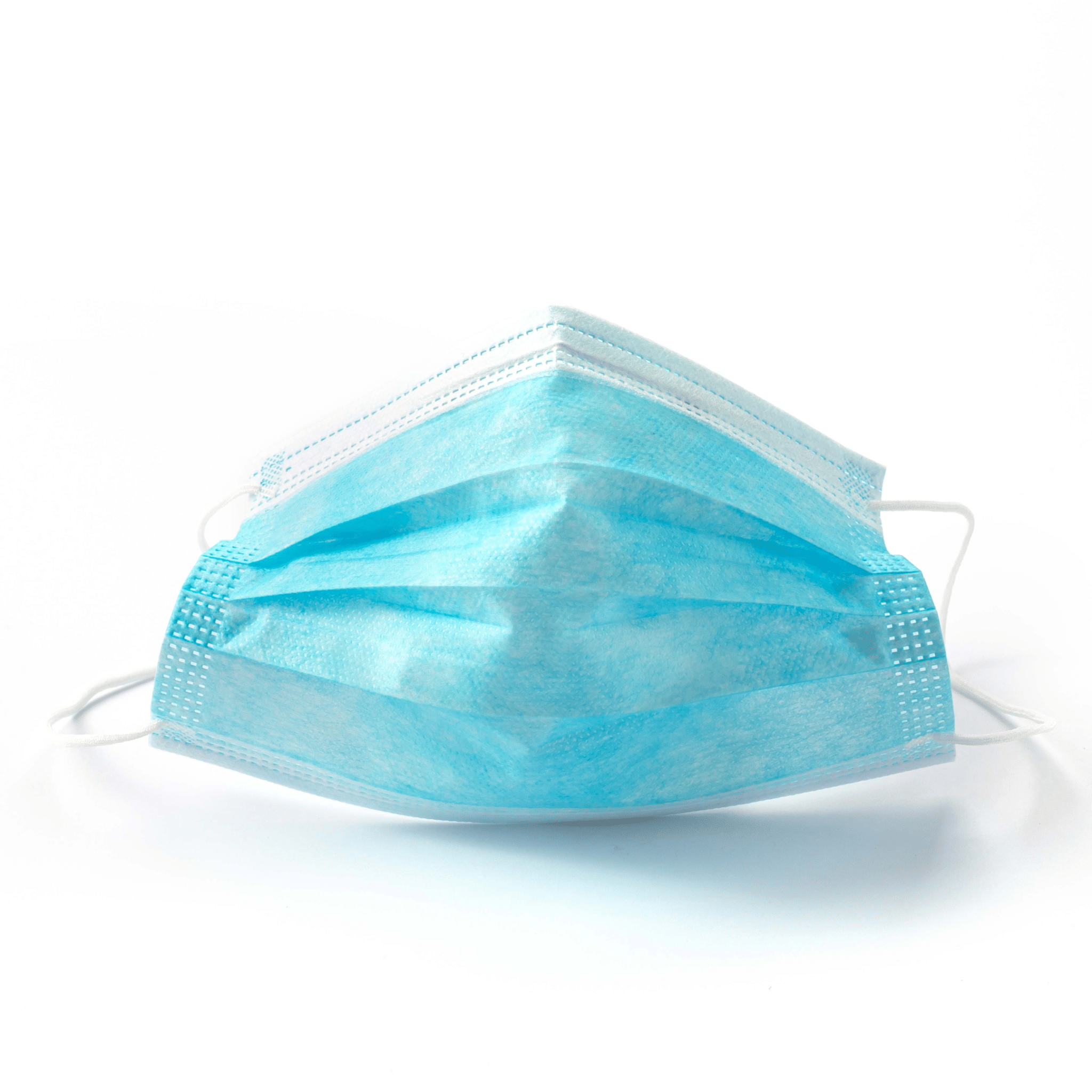
The Importance of Face Masks in Current Times
The demand for face masks has skyrocketed. They’re essential for health care workers on the front lines, protecting them and those they serve. Wear masks has become a mantra, part of our new normal.
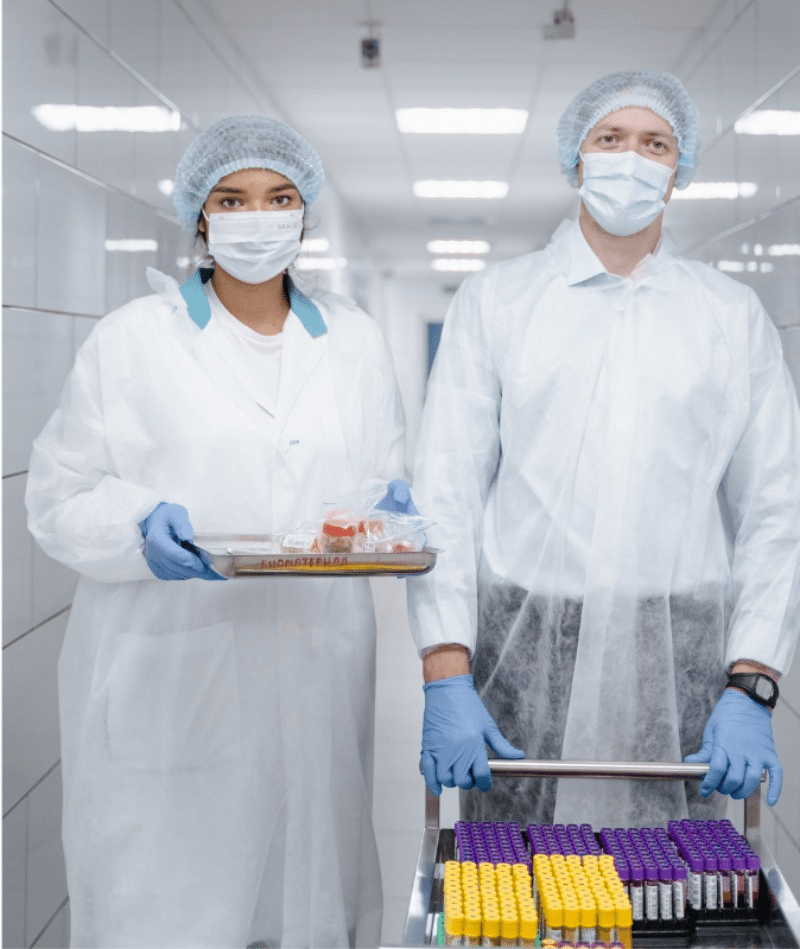
Different types of masks, from surgical masks to N95 masks, are produced to meet varied needs. Disposable face masks are popular for their convenience, while reusable face masks have gained traction for their sustainability.
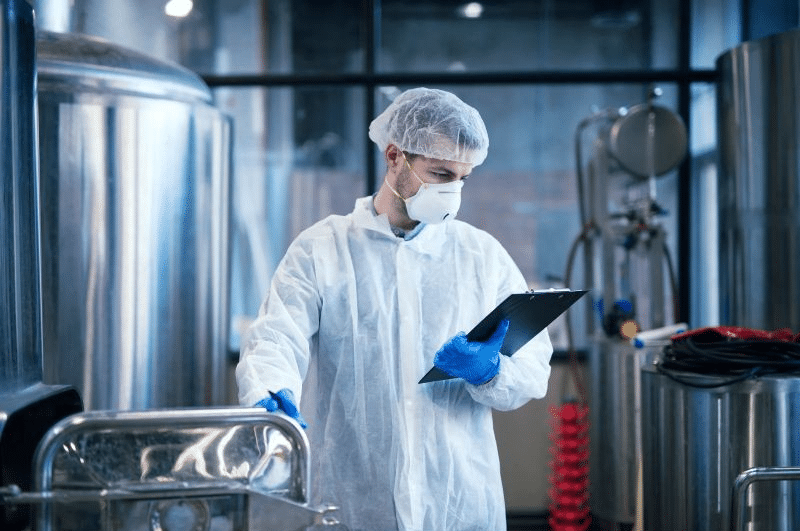
Face Mask Factory: The Hub of Production
The face mask factory is a beehive of activity. With its production lines operating around the clock, the factory works tirelessly to produce masks to meet the growing demand.
Manufacturing processes vary based on the type of mask being made. Manufacturing facilities across the globe, especially in China and the USA, have ramped up their production capacity to produce millions of masks.
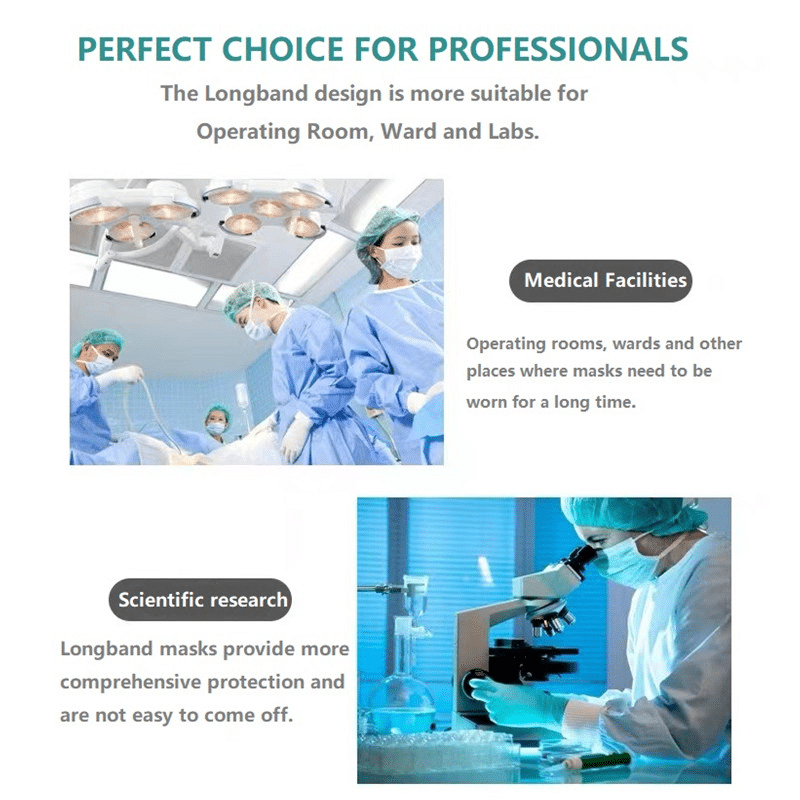
Key Components of Face Masks
Every mask, from the basic to the most specialized, typically has three layers. The outer layer is water-resistant, the middle filters out airborne particles, and the inner layer absorbs moisture from the breath.
Ear loops are another critical component, ensuring the mask fits securely on the wearer’s face.
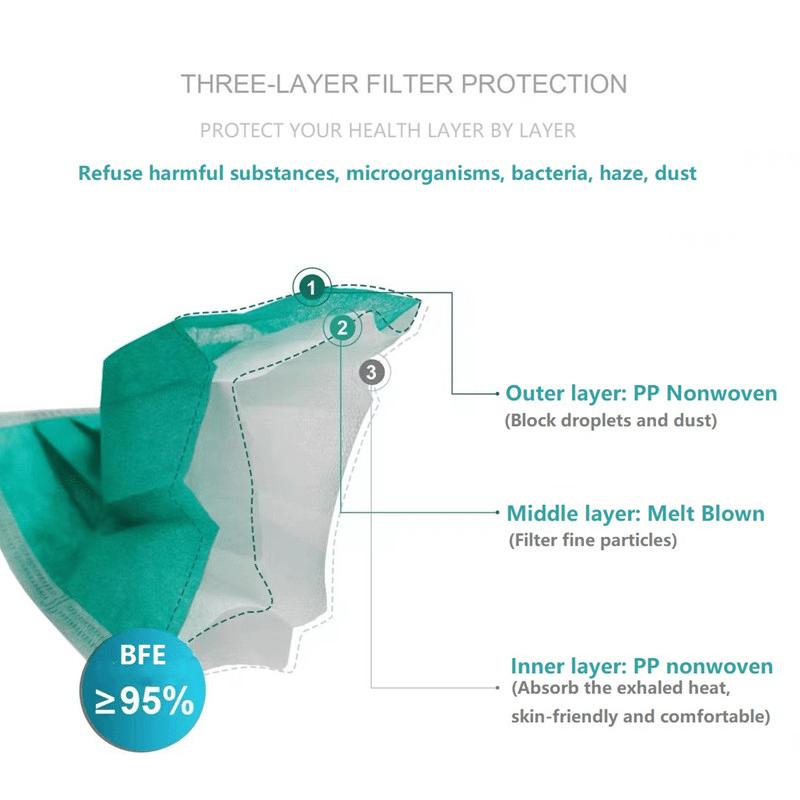
A Deep Dive into Different Types of Masks
Surgical masks, typically green or blue, have a melt-blown layer sandwiched between non-woven fabric. They provide a high level of protection against large airborne particles.
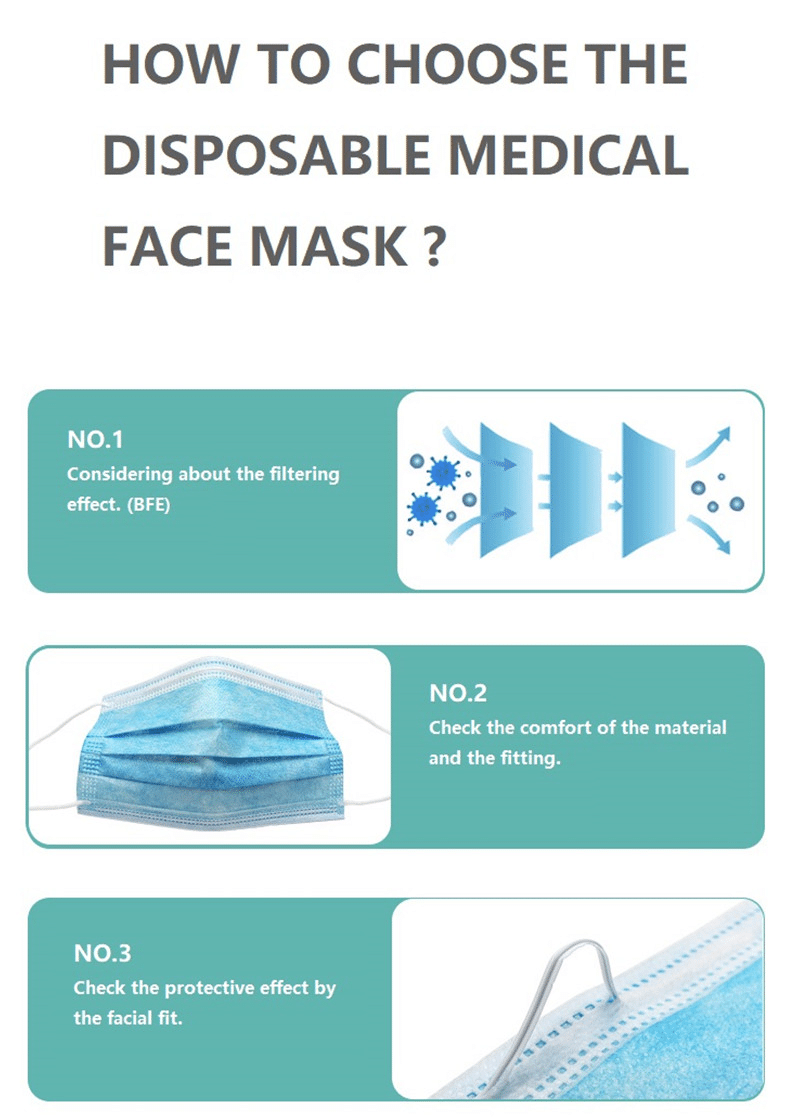
N95 masks, on the other hand, are designed to protect against smaller particles. These are often worn by healthcare professionals.
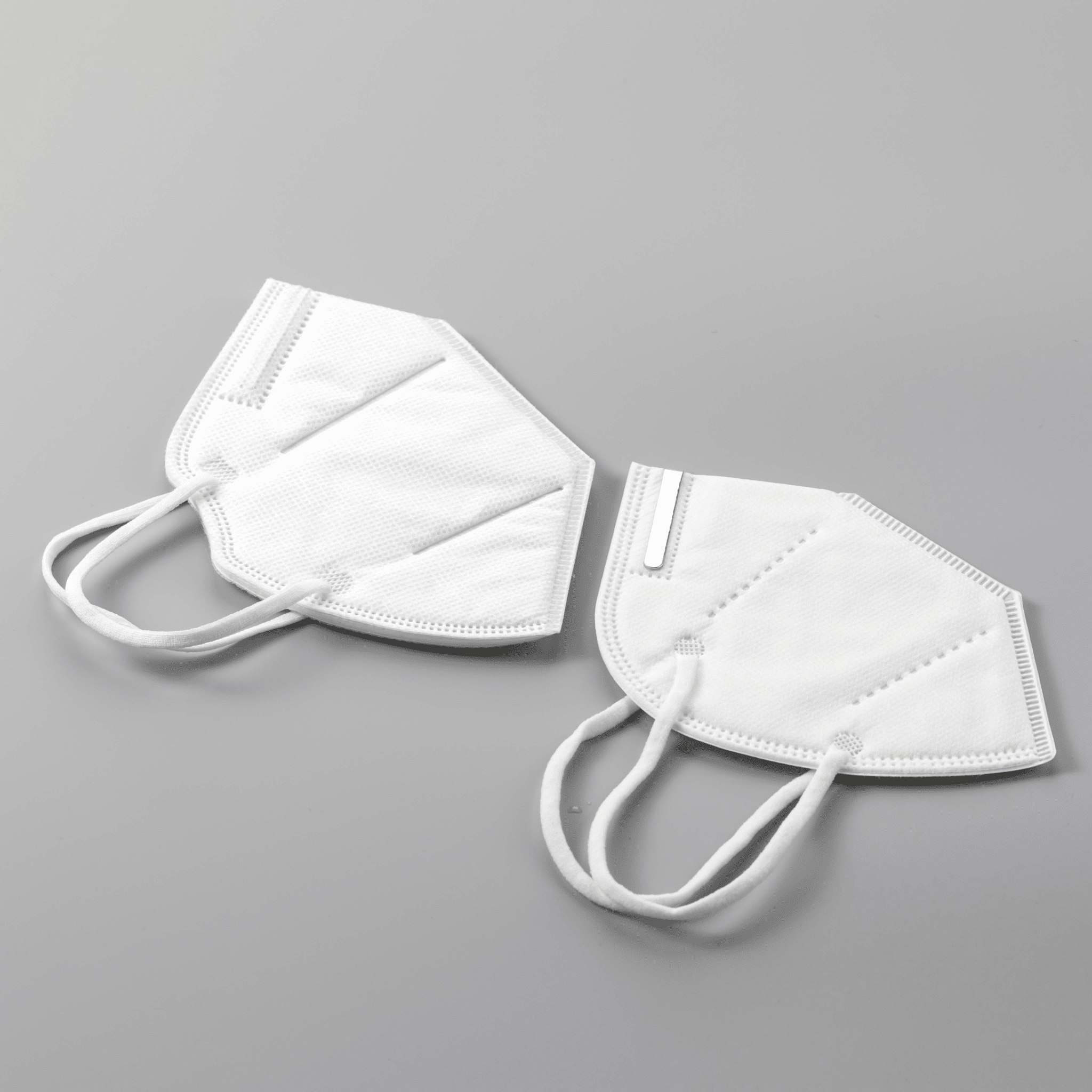
The Production Process of Face Masks
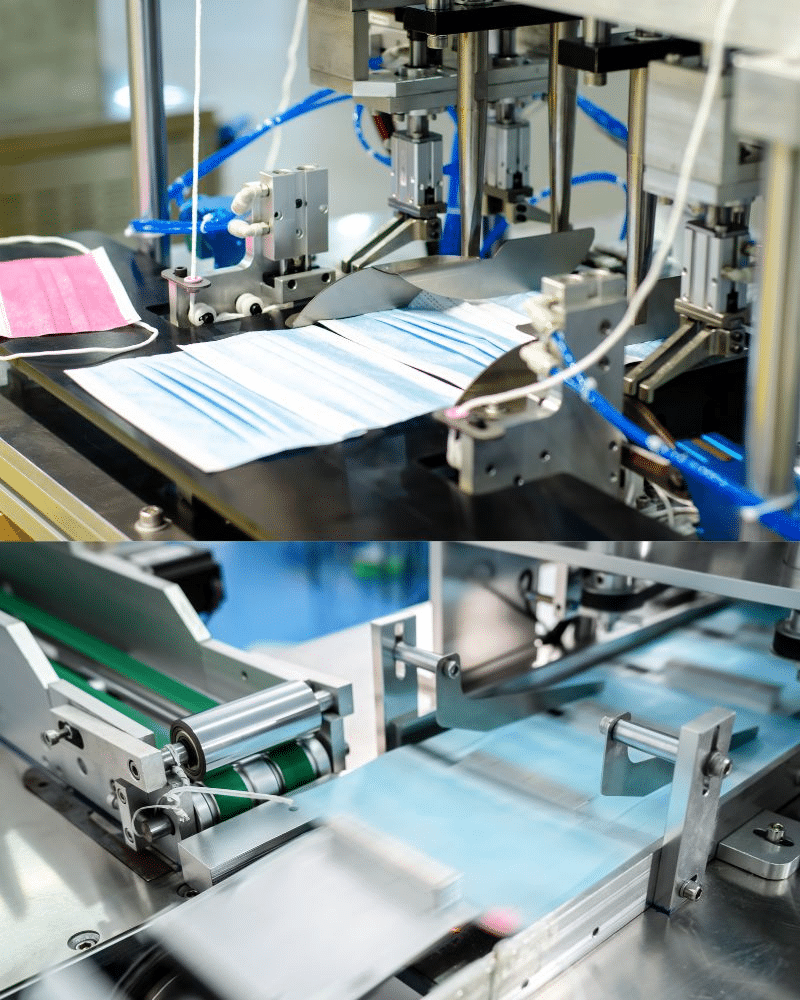
The process begins with the preparation of the materials for the three layers. Then, the layers are fed into the machine which joins them together. Ear loops are then attached, and the finished masks are packaged for distribution.
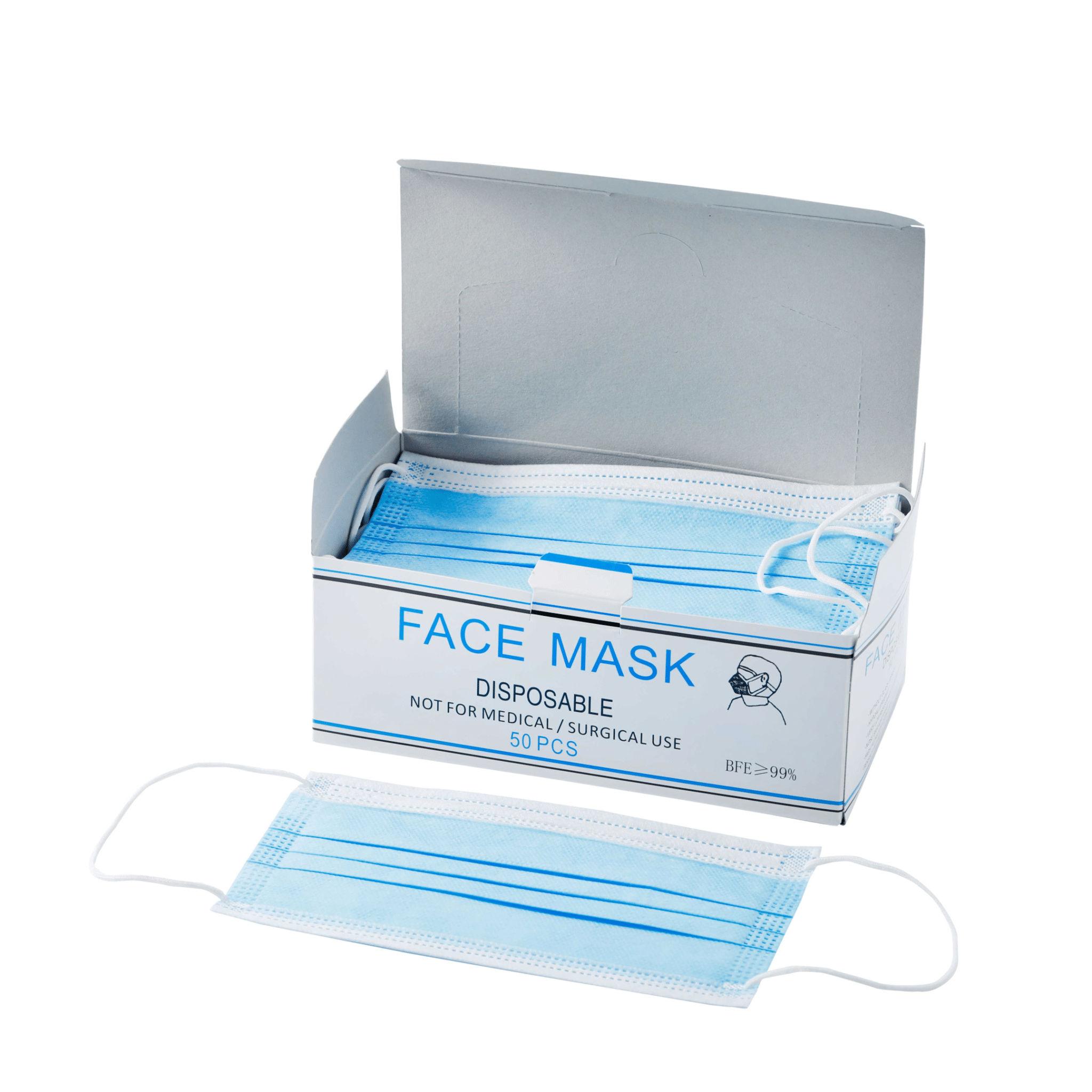
The Role of Technology and Automation in Mask Production
Advanced machines play a vital role in the production process. Automation has enabled the factory to ramp up production to meet the surging demand. Innovations include machines that can automatically attach ear loops and machines that can test the effectiveness of the mask’s filtration. These innovations help ensure that every mask maker maintains a high standard of quality.
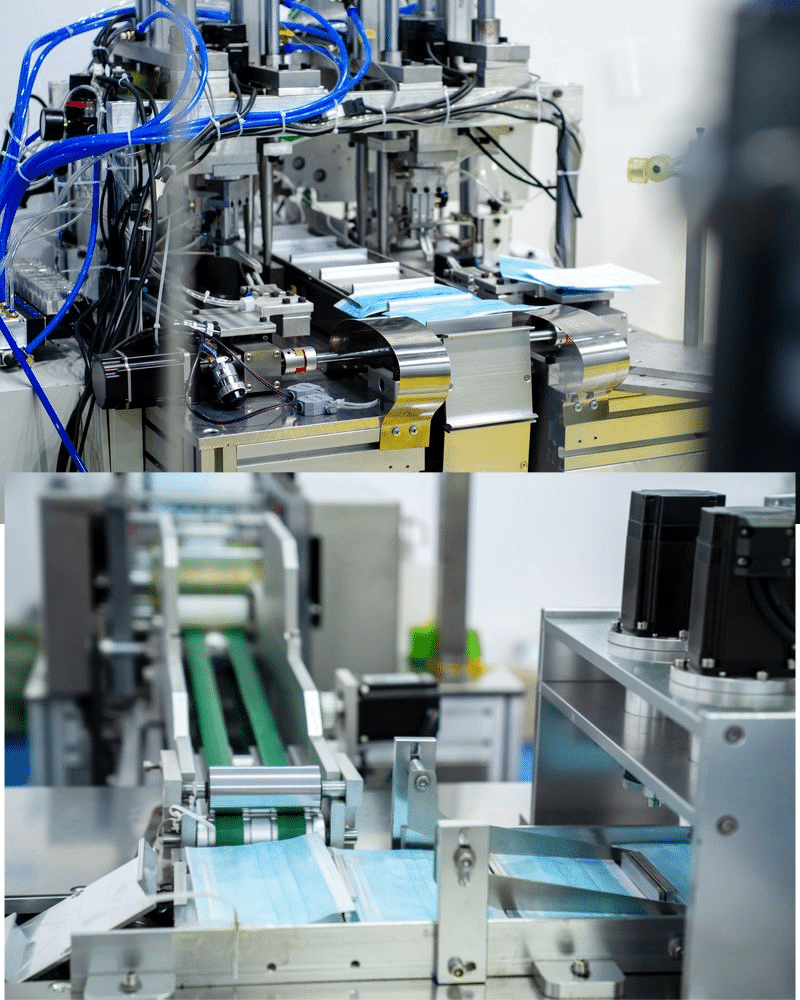
Innovation in Face Mask Production
There’s an increased focus on quality control in the mask manufacturing process. Innovative practices such as using heat-sensitive ink to validate sterilization, or incorporating biocompatible materials in the mask’s layers, are now common. These innovations provide protection not just for the wearer, but also for the environment.
The Market for Face Masks
Distributors are key in getting these masks from the factory to the customer. The pandemic has not only driven up the demand for masks but also the expectation for quality. As such, there’s an increased emphasis on safety standards and certifications such as the FDA approval in the USA.
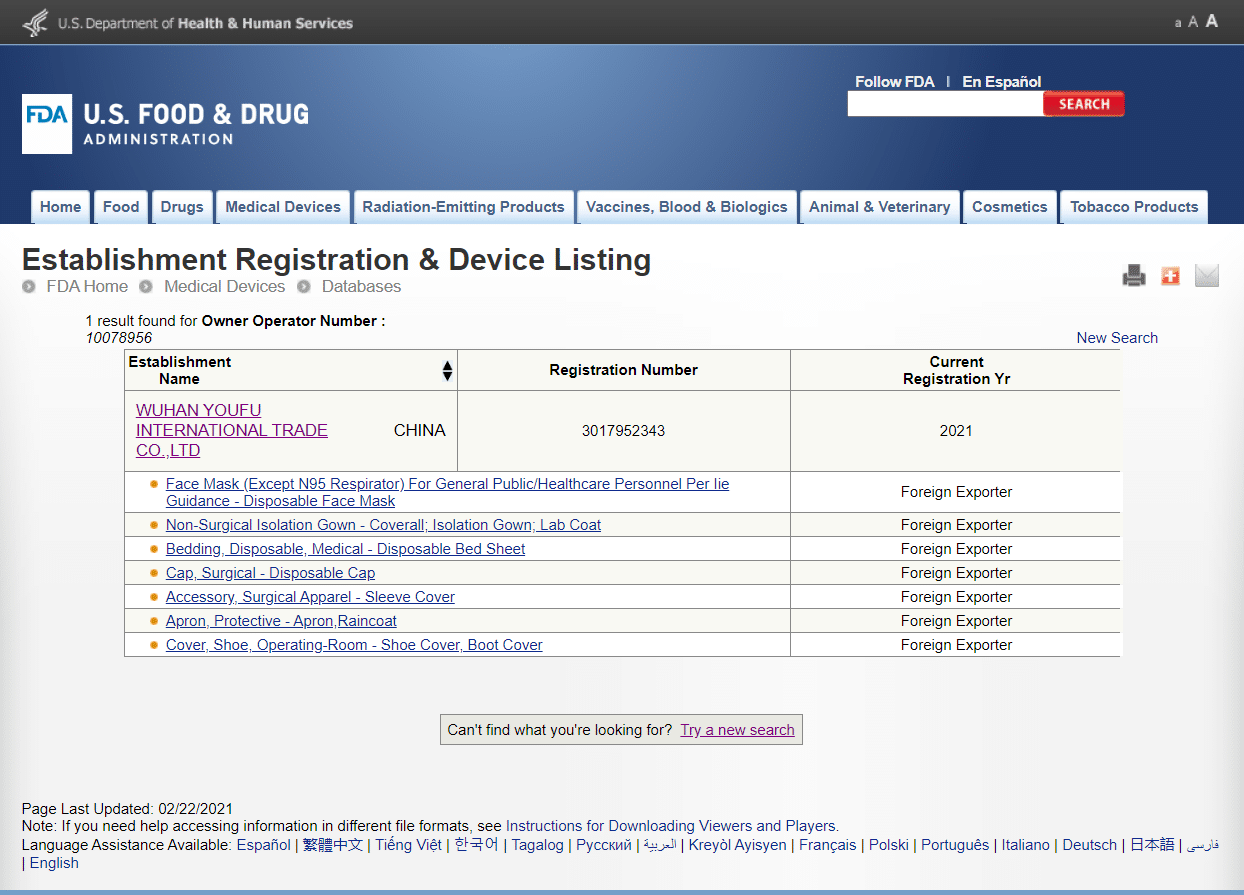
Conclusion
The face mask industry has adapted swiftly to the challenges of the pandemic, with innovations at the face mask factory playing a pivotal role. Manufacturing has ramped up to unprecedented levels, and advancements in technology and automation have ensured this production can keep pace with the demand. As we look to the future, the face mask industry’s continued innovation will undoubtedly serve as an essential pillar in global health.
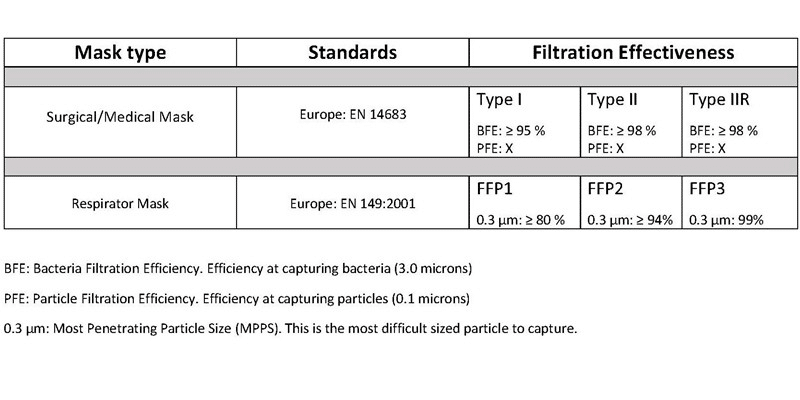
FAQs
1. What are the main types of masks produced in a face mask factory?
The main types of masks include surgical masks, N95 masks, disposable face masks, and reusable face masks.
2.What role does automation play in mask production?
Automation helps to speed up the production process, increase efficiency, and ensure consistent quality in mask production.
3.What are the key components of a face mask?
A typical face mask has three layers: an outer layer that is water-resistant, a middle layer that filters out airborne particles, and an inner layer that absorbs moisture.
4.How has the pandemic affected the face mask industry?
The pandemic has significantly increased the demand for face masks. As a result, manufacturing processes have been ramped up, and there has been an increased focus on quality and safety standards.
5.What innovations are being seen in face mask production?
Innovations include machines that can automatically attach ear loops, heat-sensitive ink to validate sterilization, and the use of biocompatible materials in mask production.