Introduction to Healthcare Compliance in Surgical Settings
When we think about surgery, the image that often comes to mind is a team clad in green or blue, focused intently over a patient. But have you ever wondered about the little cap that snugly fits their heads? It’s not just part of the “look” – that disposable surgical cap is a key player in maintaining a sterile environment. Compliance with healthcare regulations is no small feat, and these caps are at the vanguard of ensuring safety and cleanliness in the OR.
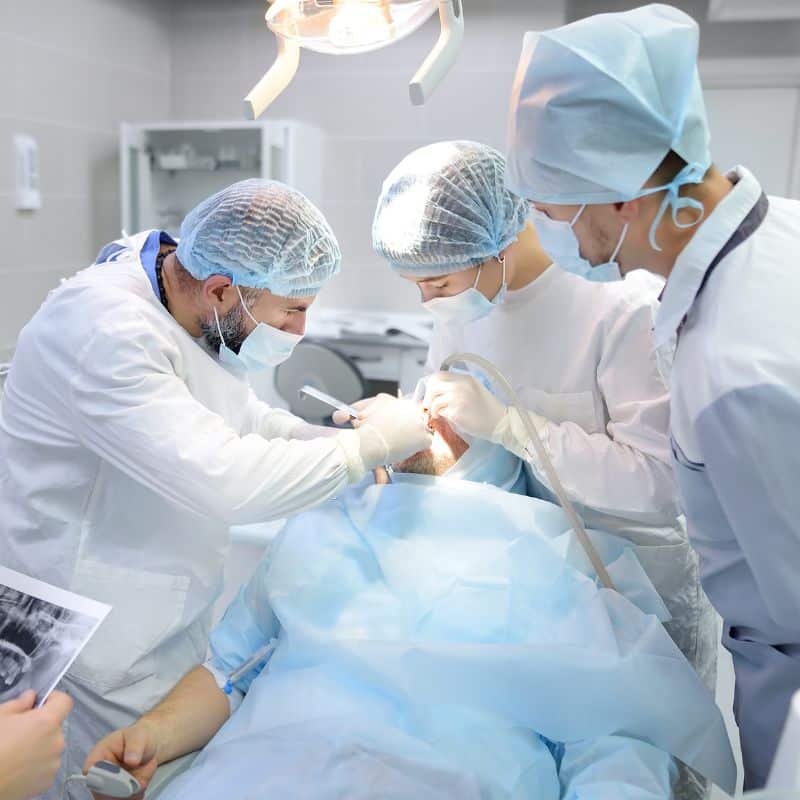
The Critical Importance of Compliance
Let’s cut to the chase – in healthcare, compliance isn’t just a buzzword; it’s the backbone of patient safety. Every thread in a surgical cap, every process in its production, is governed by strict regulations. And for a good reason. When manufacturers comply, they’re not just ticking off boxes on a checklist; they’re saving lives by preventing infections.
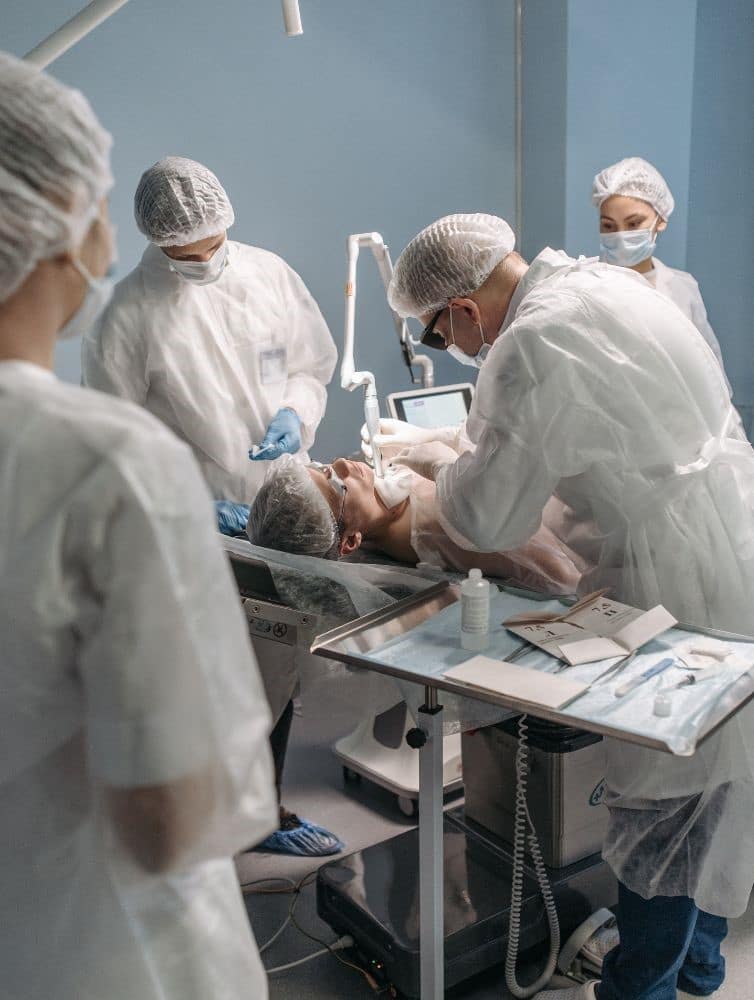
Disposable Surgical Caps at the Forefront
Disposable surgical caps might seem like simple pieces of fabric, but they’re defense champions against contaminants. They need to meet a barrage of compliance standards – and manufacturers are the gatekeepers. So, how do these unsung heroes ensure that every cap is up to snuff?
Understanding Compliance Standards for Surgical Caps
To the uninitiated, compliance standards might seem like a tangled web. But at their heart, they’re about ensuring products are safe and effective. Let’s unravel some of these threads.
The Basics of Regulatory Requirements
In the realm of surgical caps, regulations dictate everything from the materials used to the way they’re packaged. Agencies like the FDA in the U.S. or the MHRA in the U.K. lay down the law to ensure that these products don’t compromise sterile fields.
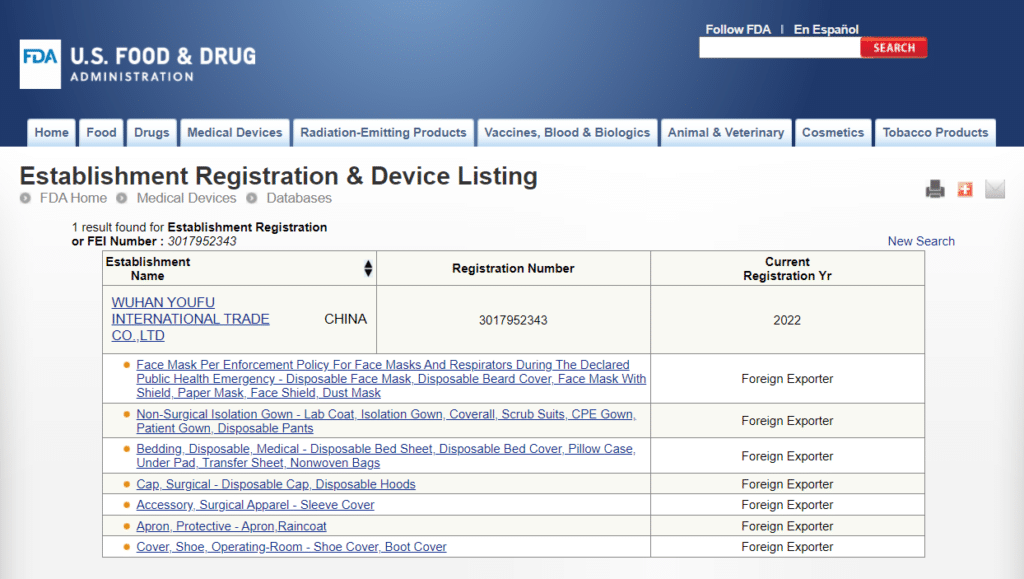
Material Standards and Quality Control
It all starts with the right fabric – one that’s breathable yet forms an impervious barrier to microbes. Manufacturers must rigorously test their materials and ensure they’re cutting the mustard every time. This isn’t a “set it and forget it” kind of deal; it’s ongoing vigilance.
The Manufacturer’s Role in Compliance
Behind every surgical cap is a manufacturer pulling the strings to ensure it meets the mark. Let’s take a peek behind the curtain.
Ensuring Sterile Production Environments
Manufacturers must create their products in conditions that would make even the cleanest person blush. We’re talking about facilities that are as sterile as the caps they’re churning out – no mean feat!
Adhering to International Standards
With healthcare being a global affair, manufacturers must play ball with international standards. It’s like juggling, but with regulations – ensuring that caps meet different countries’ standards without dropping the ball.
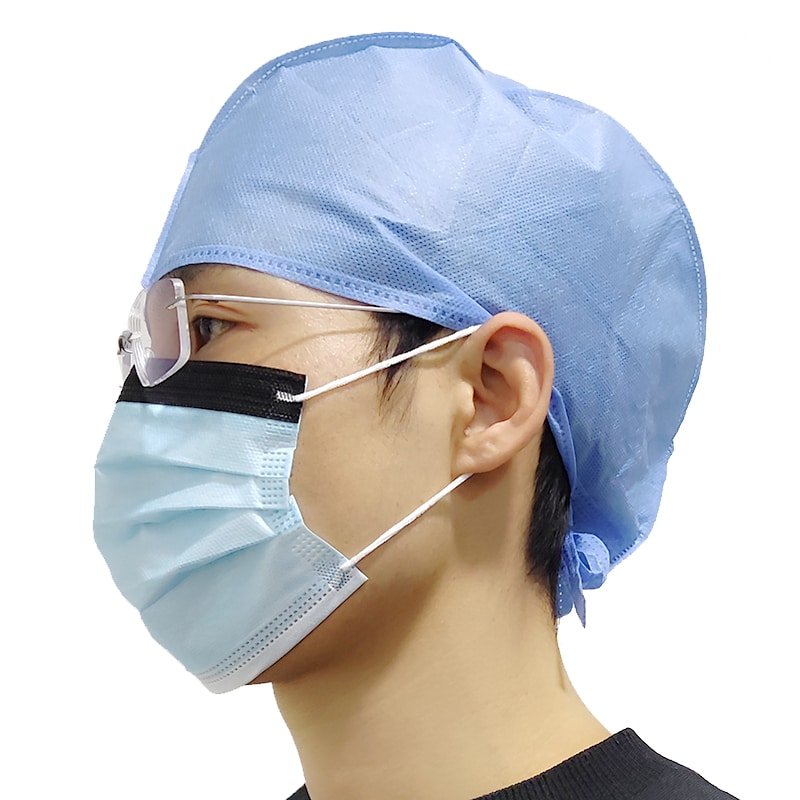
The Impact of Non-Compliance
Cutting corners in compliance is like playing with fire – you’re bound to get burned. And in this industry, burns can be severe.
Risks Associated with Non-Compliant Products
Here’s the harsh truth – non-compliant caps can be a one-way ticket to infection city. And that’s a journey no patient should take. The risks range from mild infections to severe complications. Not exactly the souvenir you want from a surgical procedure.
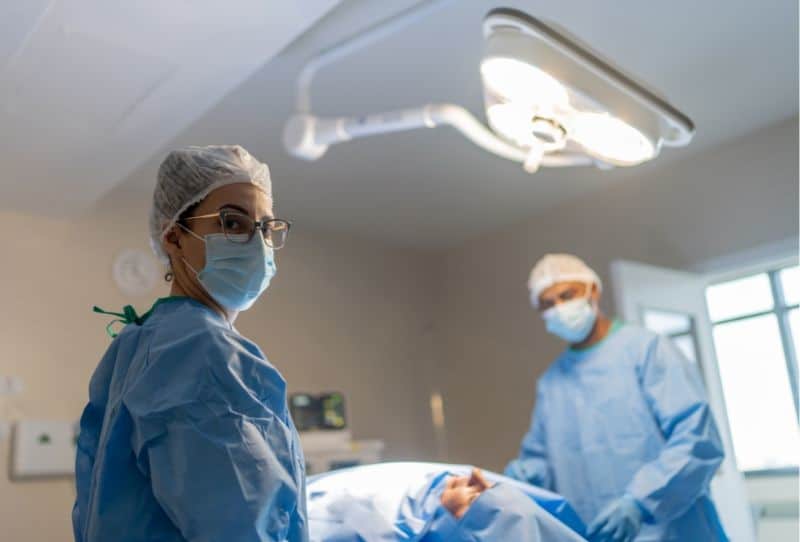
The Cost of Cutting Corners
Non-compliance can hit manufacturers where it hurts – their reputation and their wallet. Recalls, lawsuits, and loss of trust are just the tip of the iceberg. It’s a high price to pay for skimping on standards.
Navigating the Compliance Certification Process
The path to certification is paved with good intentions and a lot of hard work. Let’s walk through the steps manufacturers take to get that golden seal of approval.
Steps to Certification
It’s not just about making a great product; it’s about proving it’s great. That means jumping through hoops like audits, documentation, and a slew of tests. It’s the manufacturing equivalent of an obstacle course.
Maintaining Ongoing Compliance
Getting certified isn’t the end of the road. Manufacturers must keep their eye on the ball, constantly monitoring and updating their processes to stay compliant. It’s a marathon, not a sprint.
Innovation and Compliance: Striking a Balance
In a world that’s always changing, manufacturers have to be innovators. But how do they balance the scales between creating cutting-edge products and staying compliant?
The Drive for Better Products
Manufacturers are in a constant race to build a better mousetrap – or in this case, a better surgical cap. They’re always on the lookout for new materials and processes that can offer better protection and comfort.
Incorporating New Standards into Product Design
As new standards emerge, manufacturers have to weave these into their product designs. It’s a delicate dance between innovation and compliance, and it takes a deft hand to do it right.
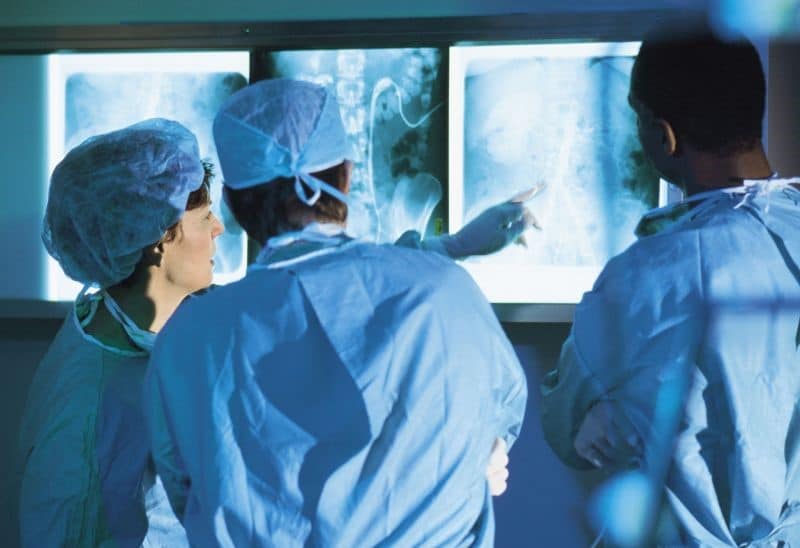
The B2B Client’s Role in Compliance
It’s not just manufacturers who need to be on their toes – B2B clients have a role to play too. They’re part of the compliance tango, and it takes two to tango.
Selecting the Right Manufacturer
For B2B clients, choosing the right manufacturer is like picking a dance partner. They need to look for partners who know the steps and can keep pace with the rhythm of regulations.
Performing Due Diligence
Due diligence is the B2B client’s homework. It means vetting manufacturers, asking the tough questions, and ensuring they’re not just compliant but consistently so. It’s a critical step that can’t be skipped.
Future Trends in Surgical Cap Compliance
The only constant in healthcare is change. Regulations will evolve, and manufacturers must be ready to adapt. What does the future hold, and how can manufacturers prepare for it?
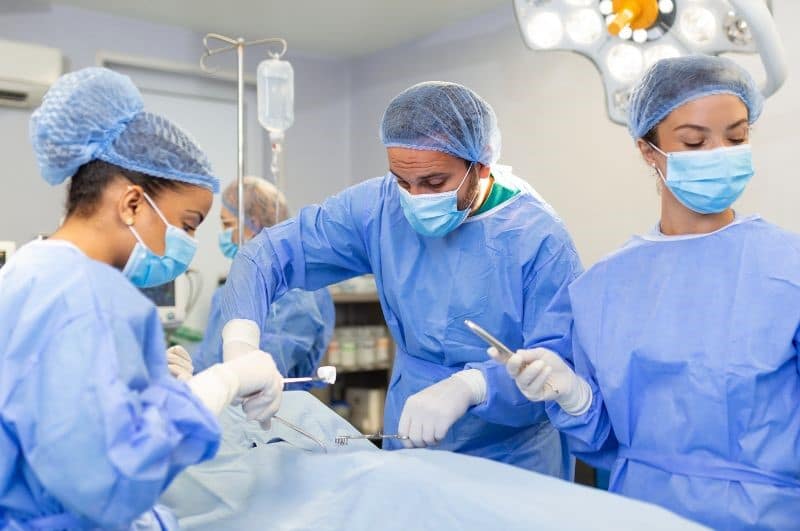
Anticipating Changes in Regulations
Staying ahead of the curve means keeping an ear to the ground for regulatory changes. Manufacturers have to be proactive, not reactive, to stay in the game.
Manufacturers’ Preparedness for Future Challenges
The best manufacturers are the ones looking to the horizon. They’re preparing for future challenges by investing in research and staying flexible. It’s about being ready for whatever comes next.
Conclusion: A Cooperative Effort for a Safer Future
In the world of healthcare, compliance is a shared responsibility. Manufacturers, B2B clients, and regulators must work in concert to ensure that the humble surgical cap continues to play its vital role in patient safety. It’s a cooperative effort that ensures a safer future for everyone.
Summarizing the Importance of Compliance
To wrap it up, compliance in the manufacture of disposable surgical caps isn’t just about meeting standards; it’s about upholding the sanctity of healthcare. It’s a commitment to patient safety and quality care.
The Path Forward for Manufacturers and Healthcare Providers
The path forward is clear – it’s paved with collaboration, innovation, and an unwavering commitment to compliance. For manufacturers and healthcare providers alike, it’s about walking this path together, with the shared goal of safeguarding health and well-being.
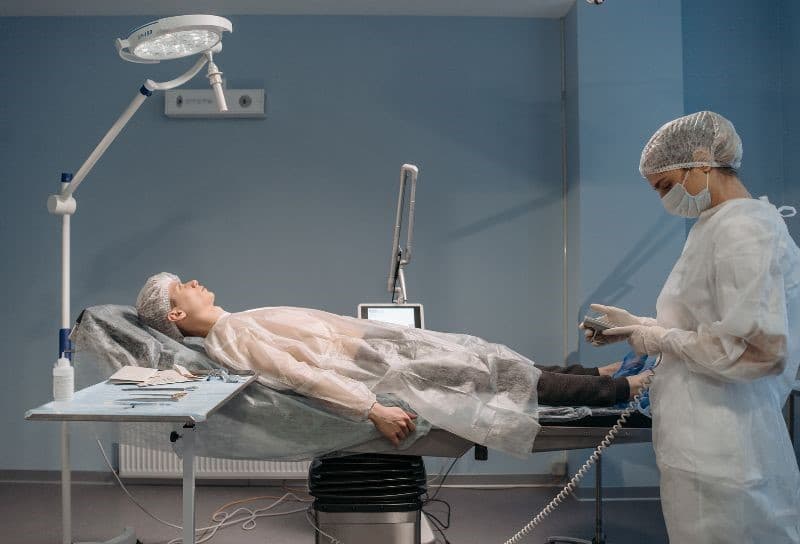
FAQs
- Q: Why is compliance so critical in the manufacture of disposable surgical caps? A: Compliance ensures that surgical caps are produced to meet strict safety and quality standards, reducing the risk of infections and ensuring patient safety in surgical settings.
- Q: What happens if a manufacturer fails to comply with healthcare regulations? A: Non-compliance can lead to serious consequences, including product recalls, legal action, financial penalties, and damage to reputation.